Table of Contents
The world moves fast. Stay ahead.
Subscribe to our newsletter for business transformation news delivered straight to your inbox.
Thank you!You've been successfully subscribed.
Share this post
Key challenges
Fragmented Network: Fragmented Victorian DC network with multiple DCs inherited from the consolidation of acquired businesses.
Capacity Constraints: Existing facilities at capacity, limiting growth opportunities.
Suboptimal Processes: Suboptimal business processes due to aged IT systems and legacy ways of working that couldn't scale to support increasing volume.
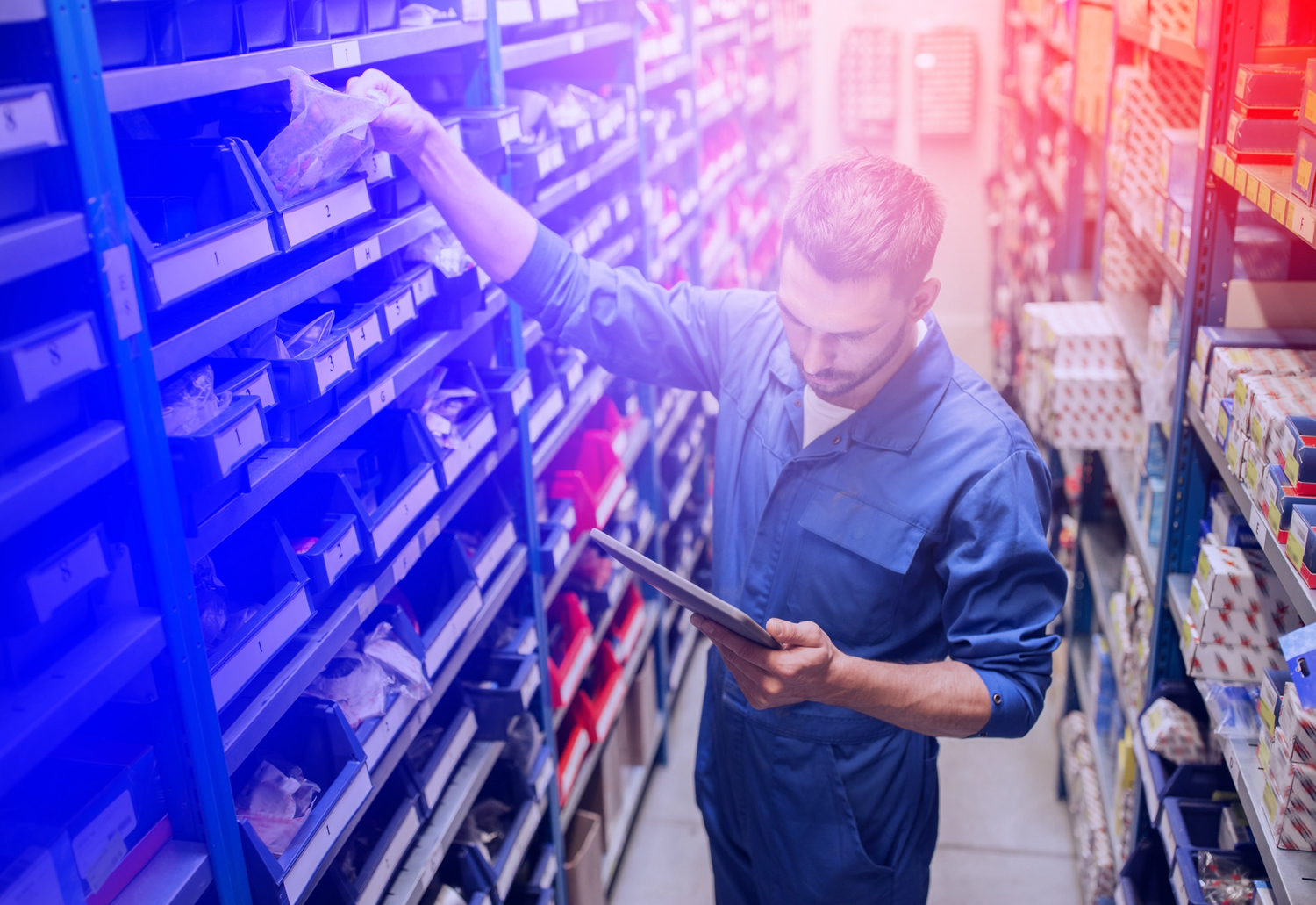
Our approach
Following the successful completion of a significant network strategy, Bapcor enlisted TMX to spearhead the design and procurement of a new 50,000sqm (538,195sq ft) DC in Melbourne, aiming to consolidate multiple existing facilities across metropolitan Melbourne.
Here is what TMX delivered for our client:
- Comprehensive project management by populating a detailed statement of requirements, approached the market at large, shortlisted responses, and negotiated terms with the preferred developer.
- Procured and developed a new, fully optimized distribution center designed to be best in class.
- Designed, developed, and delivered end-to-end business processes to enable multiple Business Units.
- Specified and procured all major components, including WMS, automation systems, MHE, and racking.
- Led and coordinated the program PMO, ensuring all stakeholders were briefed and engaged throughout the process.
The results
- Successfully secured the new Melbourne DC at a competitive "effective" rental level.
- Achieved practical completion of the facility in 2020, on time and within budget, with minimal disruptions despite COVID-specific delays.
- Implemented extensive integration of GTP automation technology, facilitating the processing of 4,200 order lines per hour.
- Executed a seamless transition that met full-service targets from day one, ensuring operational readiness.
- Rapidly increased DC operations to meet and sustain target performance levels.
The world moves fast. Stay ahead.
Subscribe to our newsletter for business transformation news delivered straight to your inbox.
Thank you!You've been successfully subscribed.